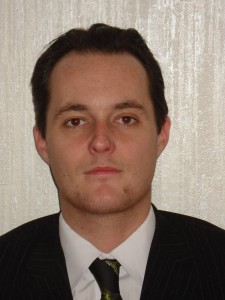
GAMUS DÁNIEL, IMEX Filtertechnika Kft. Sopron
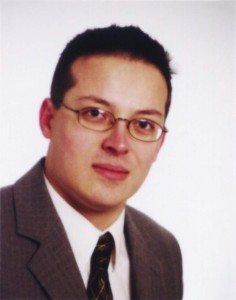
HORVÁTH ANDRÁS, Műszaki szakértő MÁV-TRAKCIÓ Zrt.
Szűréstechnikai alkalmazások a vasútüzemben
1. rész
A vasútüzemi dízelmotorok szűrői
Összefoglaló:
Az utóbbi években a dízelmotorok az egyre szigorodó környezetvédelmi követelmények, valamint az üzemeltetés és a karbantartás növekvő igényeinek hatására komoly fejlődésen mentek keresztül. Az új fejlesztések robbanásszerű előretörése ma már jól érzékelhető a vasúti járművek esetében is: a bekerülési költségekkel szemben egyre inkább előtérbe kerül a gazdaságos és főleg takarékos üzemeltetés. Az élettartam növelésének, a folyamatosan alacsony tüzelőanyag fogyasztásnak, az időszakos karbantartási költségek minimalizálásának alapvető feltétele a gondos tervezés, a felhasznált anyagok kiváló minősége. A legfontosabb tényező – mint az élet sok más területén – a megelőzés, melynek elengedhetetlen eszköze a szűréstechnikai berendezések megfelelő kiválasztása.
A szűréstechnika a vasútüzem szinte minden területén jelen van, a vontatójárművek gépeinek fontos, nélkülözhetetlen elemei szűrőberendezések (dízelmotorok levegő-, üzemanyag-, kenőanyagszűrői, tengelykapcsolók, hajtóművek, hidrosztatikus rendszerek szűrői, légsűrítők, levegős rendszerek szűrői), de különféle szűrőberendezések megtalálhatók személykocsik, mozdonyok klímaberendezéseiben vagy a vontatási telepek, járműjavítók műhelyeiben (hegesztési füstelszívók, porleválasztók, olajköd-leválasztók).
A szűrőrendszerek alkalmazásának általános célja a nagyértékű gépek, berendezések védelme a szennyeződésektől, a szennyeződések által okozott üzemzavaroktól, károktól és az elvárt élettartamnál korábbi tönkremeneteltől. A szűrők feladata, hogy a felhasznált és a kibocsátott közegből (pl. levegő, kenőolaj, üzemanyag, hidraulika-folyadék, kipufogógáz stb.) azt a káros frakciót kiválasszák vagy kiszűrjék, amely valamilyen módon túlzott elhasználódást, többletköltséget, környezetkárosítást okoz.
A modern vasútüzem által támasztott követelményeknek és az Európai Unió egyre szigorodó környezetvédelmi szabályozásának a szűrőgyártók újabb és újabb fejlesztésekkel tudnak megfelelni. A rendkívül széles alkalmazási terület miatt a következő cikkekben csak a legfontosabbnak tartott és a legkorszerűbb alkalmazások kerülnek bemutatásra.
I. A levegőszűrés szükségszerűsége és technikái
A belsőégésű motorok üzeméhez jelentős mennyiségű levegő szükséges. A motor által beszívott környezeti levegő minősége, szennyezettsége jelentősen befolyásolhatja a motor üzembiztonságát, az egyes alkatrészek és a motor élettartamát. Ezért feltétlenül szükség van a motorban felhasznált levegő nagyon pontos szűrésére. A motorok megbízható üzemének egyik alapfeltétele, hogy a motorba csak pormentes és tiszta levegő kerülhet!
A környezetünkben található levegő többé-kevésbé szennyezett, a szennyeződések legkülönbözőbb fajtái, mint pl. por, füst, korom stb. találhatók benne. A levegőben található szilárd szennyezőanyagok eredetüket tekintve két csoportra oszthatók: a talajból, a környezetből kivált szemcsékre (por) és a motorban az üzemanyag elégetésekor keletkezett szilárd szennyeződésekre (korom).
A levegőben található szilárd szennyezőanyagok közül a finom por 1-5 μm, a közepes por 5-10 μm, a nagy szemcsés por 10-50 μm, a durva szemcsés por 50-250 μm méretű részecskékből áll, míg a koromrészecskék 1 μm alatti méretűek is lehetnek.
Az 5 μm-nél kisebb méretű porszemcsék akár több órán keresztül is a levegőben lebeghetnek, a nagyobb méretű szemcsés por percek alatt leülepedik a talajra.
A levegőben szálló por összetétele általában 75% SiO2 kvarchomok, 15-20% szerves szennyezők és vegyületek, 5-10% különféle fémoxidok CaO2, MgO, Fe2O3, Al2O3.
A szilárd szennyeződések közül a belsőégésű motorok üzemére a kvarcpor a legveszélyesebb a henger, dugattyú, dugattyúgyűrű, csapágyak kopását, elhasználódását felgyorsító hatása miatt. A vasútüzem sajátossága, hogy pályaudvarok, forgalmas vasútvonalak környékén a fémpor (féktuskópor) általában magasabb arányban található meg a levegőben.
A levegőszűrés szükségességét a következő példával lehet érzékeltetni: egy 1000kW teljesítményű, 200 g/kWh fajlagos fogyasztású vasúti dízelmotor óránként közelítőleg 2400 m3 levegőt használ (1 kg üzemanyag elégetéséhez 15,4 kg, azaz kb 12 m3 levegő szükséges). Feltételezve, hogy a beszívott levegő átlagos portartalma csak 0,001 g/m3 (ami gyenge portelítettséget jelent) a motorba szűrés nélkül 2,4 g pormennyiség kerülne óránként. Évente 3500 üzemórás működést feltételezve közelítőleg 8,4 kg por kerülhetne a példában szereplő motorba. Nyilvánvaló, hogy a létező legjobb és legdrágább motorolaj sem lenne képes ezt a pormennyiséget kezelni, levegőszűrés nélkül a motor idő előtt elhasználódna. Ezért a motorok elvárt élettartamának teljesüléséhez a lehető legjobb leválasztási fokkal rendelkező és jól működő (az előírt ciklusrend szerint cserélt) légszűrő használata elengedhetetlen.
A példában szereplő motorra szerelt levegőszűrőnek legkevesebb 8,4 kg por motorba jutását kell megakadályoznia évente, így világosan látszik, hogy egy „csupán” 1-2 %-kal gyengébb hatásfokú légszűrő alkalmazása is jelentős különbséget jelent pormennyiséget illetően.
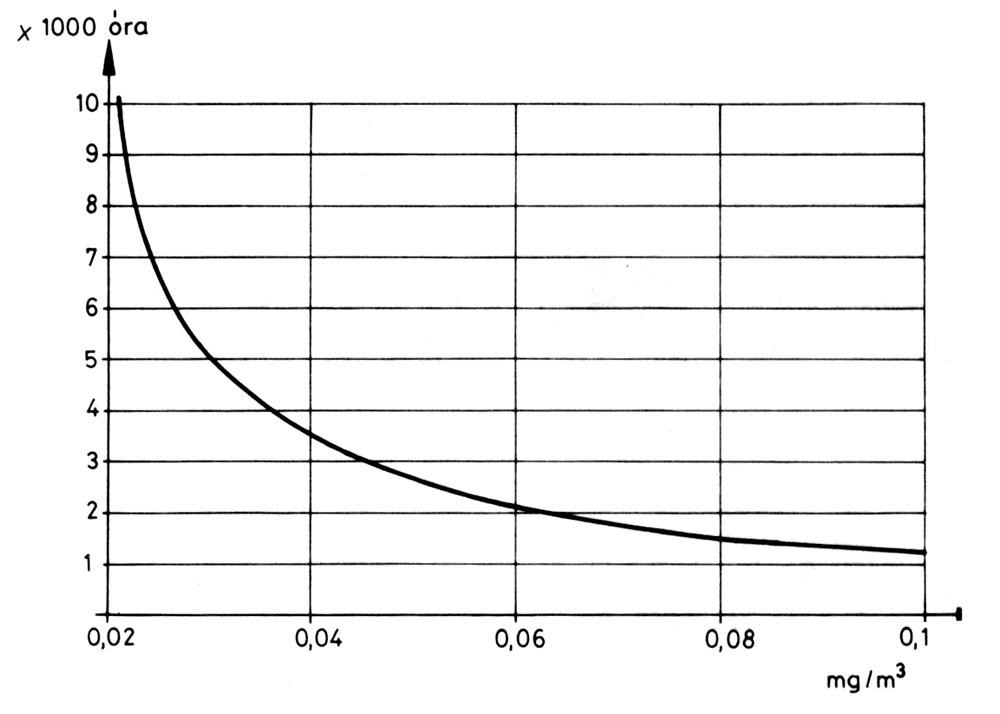
A dízelmotor által a levegővel beszívott por mennyiségének és a motor élettartamának összefüggései
Picture 1:Coherences between lifespan of the engine and the volume of dust suction by diesel engines
Bild 1.:Zusammenhang zwischen Motorlebensdauer und angesaugter Staubmenge bei einem Dieselmotor
Működési elvüket tekintve több fajta levegőszűrőt különböztetünk meg. Olajos légszűrők: a legegyszerűbb kialakítása az olajos vasforgáccsal töltött légszűrő, ahol az olajos felületen megtapad a por. Az olajos légszűrők fejlettebb változatai az olajfürdős vagy olajtükrös légszűrők, működési elvét tekintve hasonló működésűek: a por megkötése az olaj felületén történik. Hátrányuk a kis szűrési hatásfok (70-80%), jelentős karbantartási igény valamint az olajkihordás a levegőáramlás hatására.
A centrifugális vagy inercia levegőszűrők egyszerű szerkezetű szűrők, a szűrő járataiban a levegő irányváltoztatását használja ki a por leválasztására, általában előszűrőként használható. Hátrányaként említhető, hogy ellenállása a levegőmennyiséggel növekszik, a szűrés hatásfoka függ a szállított levegőmennyiségtől, a finom port nem szűri ki a levegőből.
Hatékonysága miatt napjainkban – néhány kivételtől eltekintve – kizárólag úgynevezett papír légszűrők alkalmazása elterjedt, melyeket más néven száraz légszűrőknek nevezünk. Motoroknál, kompresszoroknál, vákuumszivattyúknál egyaránt alkalmazzák, mivel leválasztási hatásfoka laboratóriumi mérések szerint a 99,99 %-t is elérheti. A szűrőbetétek gyakran környezetbarát kialakításúak, az elhasznált betétek hulladékégető kemencékben mindössze néhány százalék hamu visszamaradásával megsemmisíthetők.
A száraz vagy papír levegőszűrők fejlődésének főbb állomásai
A múlt század elején az amerikai farmerek folyamatosan küszködtek a porral, melyet traktorjuk motorja munka közben beszívott, az alkalmazott olajos levegőszűrők ellenére. 1915-ben Frank Donaldson kifejlesztett egy az addigiaktól merőben eltérő, szárazon működő levegőszűrőt, ahol a szűrőközegként papírt alkalmazott. A megalakult Donaldson vállalat részére a folyamatos fejlesztések eredményeképpen egyenes út vezetett a mezőgazdaságból előbb a bányaipari, majd a közúti és vasúti használathoz.
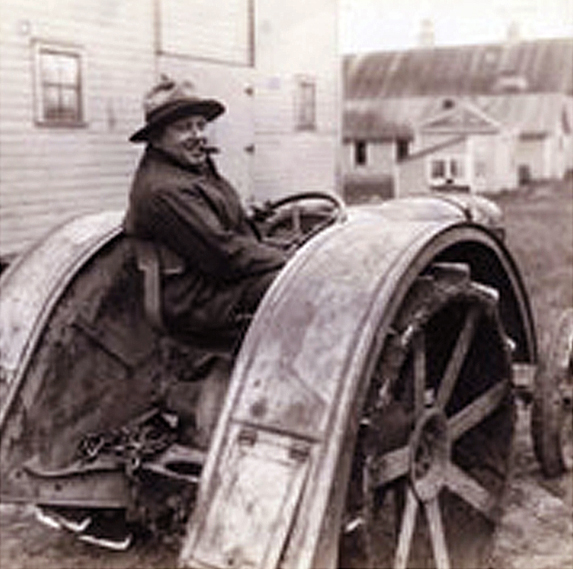
Frank Donaldsob és az első száraz levegőszűrős traktor
2. ábra: Frank Donaldson és az első száraz levegőszűrős traktor
Picture 2: Frank Donaldson and the first tractor with dry airfilter
Bild 2: Frank Donaldson und der erste Traktor mit Trockenluftfilter
A papírszűrő sikerének titka az olyan előnyökben rejlett, mint például a nagy leválasztási hatásfok (a legjobban kialakított szerkezetek, valamint a legjobb szűrőanyagok mellett a 99,99 %-os hatásfok ma már alapkövetelmény), a kompakt kialakítási mód, minden beépített helyzetben (vízszintes, függőleges) hatékony működéssel; egyszerű és tiszta karbantartást tesz lehetővé, csupán a szűrőbetétet kell kicserélni, a szűrőbetét cseréje akkor esedékes, ha az eltömődésjelző azt jelzi; ellentétben az „olajos” szűrőkkel nincs gond az elhasznált olaj elhelyezésével (veszélyes hulladék).
A levegőszűrők fejlődésének egy jelentős állomása volt a szintén a Donaldson által fejlesztett Pleatloc™ System, melyet ma minden gyártó alkalmazni próbál a szűrőbetétjeinél. A Pleatloc™ egy olyan speciális hajtogatási eljárás, amelynél egy, a szűrőpapírba nyomott keresztél távolságtartó funkciója megakadályozza a papírredők egymáshoz tapadását. Ennek különösen akkor van jelentősége, ha a papír (a levegő) nedves. A rendszer így mindig biztosítani tudja, hogy a teljes szűrőfelület mindig rendelkezésre álljon. A rendszer előnyei: a papírredők össze nem tapadása folytán a betét élettartama alatt a teljes szűrőfelület rendelkezésre áll, a szűrő 100 %-os kihasználása kiváló szennyeződés felvevő képességet és magas leválasztási hatásfokot eredményez, a szűrőbetétek élettartama 30-50 %-kal hosszabb, a karbantartás költségek jelentősen csökkennek.
Az egyre komolyabb alkalmazások és kihívások a szűrőgyártókat is új megoldásokra sarkallták. A leválasztási fok növelése érdekében a szűrő tiszta oldalát is vizsgálni kezdték. A fejlesztésekben ismét a Donaldson állt elő egy szabadalommal, a RadialSeal™ tömítéssel rendelkező levegőszűrővel. A tömítéseknek meg kell akadályozniuk, hogy a szűrőház tiszta oldalára ill. a szívócsővezetékbe falslevegőn keresztül por kerülhessen. Légszűrőbetéteknél két fajta tömítési módot különböztetünk meg: az első az axiális, tengelyirányban tömítő szűrőbetétek képviselik a régebbi, hagyományos konstrukciót, amelyet még ma is előszeretettel alkalmaznak a szűrőgyártók. Itt egyrészt a tömítés keresztmetszete, másrészt a ragasztás és a ragasztóanyag milyensége meghatározó. A nem megfelelően rögzített tömítések az időjárás ill. az erős vibráció miatt leválhatnak, s a motorba por és más szennyezőanyag kerülhet.
A második a Donaldson által kifejlesztett radiális, sugárirányban tömítő szűrőbetétek alkotják a légszűrők új generációját, s töltenek be egyre fontosabb szerepet a szűréstechnikában. A radiális tömítés teljesen megváltoztatta a szűrőbetétek felépítését, mindezt gumi, fém és ragasztóanyag nélkül.
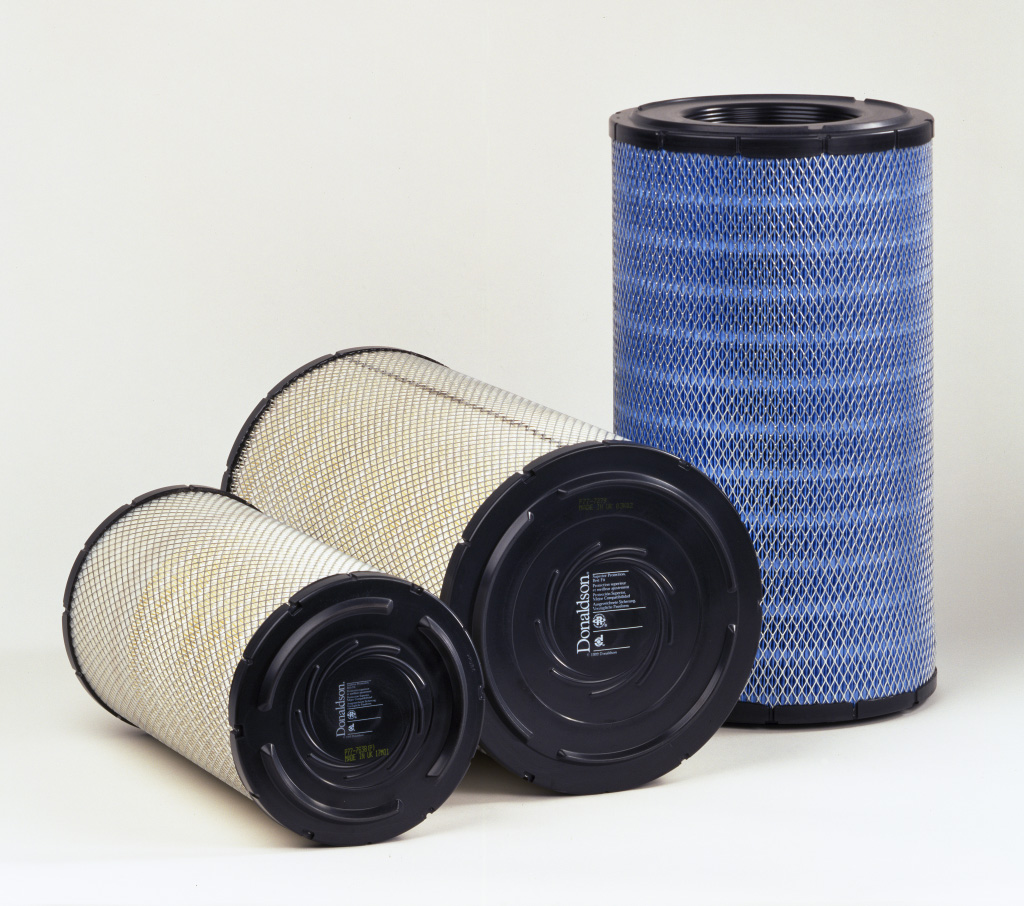
RadialSeal tömítéssel ellátott levegőszűrők
Picture 3: RadialSeal™ airfilter elements
Bild 3: RadialSeal™ Luftfilterelemente
A RadialSeal™ szűrők esetében a szűrőpapír közvetlenül a puha műanyagból készült tömítőanyagba kerül, s ebből az anyagból készülnek a szűrőbetét zárófedelei is. A tömítés és a zárófedél egy darabból áll. Ezzel a korszakalkotó felfedezéssel a Donaldson nemcsak egy újfajta szűrőbetét-sorozatot hívott életre, hanem egy teljesen új műanyag ill. műanyag-fém alapanyagú szűrőház-generációt teremtett. A gyártásukkor lényegesen kevesebb éghetetlen anyag kerül beépítésre, amely későbbi megsemmisítésüket könnyíti meg. A RadialSeal™ szűrők előnyei közt említhetjük a jelentősen nagyobb tömítőfelületet, hogy a tömítetlenség kockázata minimális, egyszerű karbantartást tesz lehetővé, a felhasznált anyagok száma lecsökken, és hogy környezetbarát.
A fenti forradalmi konstrukciók létrehozása vezetett odáig, hogy több motorgyártó világcég a Donaldson levegőszűrők mellett döntött. A Caterpillar, a Detroit Diesel, a John Deere, a Perkins, a Volvo és más vállalatok mind Donaldson gyártmányokkal hozzák forgalomba termékeiket. A közelmúltban a MÁV remotorizálási programban beépített Caterpillar motorok szintén gyárilag Donaldson szűrőházakkal és betétekkel készültek.
Egyedi (iparvasúti) mozdony átépítéseknél is gyakran találkozhatunk a modern levegőszűrőkkel. A kilencvenes években az eredeti darabok elégtelen hatékonysága miatt több iparvasúti M31DHM tolatómozdonyra kerültek Donaldson FRG légszűrőházak (17/24 VE 450 lóerős Ganz-motor), a V12-es motorokra hengersoronként egyet-egyet építettek fel. A Detroit Diesel hathengeresekkel remotorizált darabok esetén (szintén 450 lóerős) a motorfelépítés miatt elegendő volt egyetlen Donaldson ERB ház. Ez utóbbi megoldás került alkalmazásra a szintén Detroit Diesel-re átépített M43LDH (eredetileg MB836 motoros) tolatómozdonyok esetében.
4.ábra: Remotorizált M31DHM tolatómozdony komplett levegőszűrő átépítéssel
Picture 4: Remotorized M31DHM yard locomotive with reinstalled airfilter housings
Bild 4: Eine remotoriserte Schublokomotive Type M31DHM mit umgebautem Komplett-Luftfilter
5.ábra: Levegőszűrő átépítés Ganz motoros M31-en
Picture 5: Airfilter convertation on Ganz engined M31
Bild 5: Luftfilterumbau an der Lokomotive Type M31 mit Ganz-Motor
A jelen illetve a jövő szintén új technológiákat igényelt. A Donaldson 1999 óta egyre szélesebb körben alkalmazza a mind formájában, mind anyagában egyedülálló PowerCore™ rendszerű levegőszűrőket. Napjaink egyik jellemző tendenciája a járműfelépítmények egyre magasabb fokú áramvonalazottsága, ugyanakkor a motorok mérete a növekvő teljesítmény és a környezetvédelem miatt szükséges segédberendezések miatt ugrásszerűen növekszik. A PowerCore™ levegőszűrő rendszerek nagyságrendekkel kevesebb helyet igényelnek azonos teljesítmény mellett, ugyanakkor kialakítás szempontjából teljesen szabadon variálhatók, és mivel fém alkatrészeket egyáltalán nem tartalmaznak, sokkal könnyebbek, könnyebben kezelhetők. A szűrőbetétek a Donaldson által szabadalmaztatott UltraWeb™ anyagból készülnek, ami adott szállítási teljesítmény mellett tízszer hatékonyabb szűrést tesznek lehetővé sokkal kompaktabb formában, a hagyományos cellulóz alapú, hajtogatott szűrőanyaggal szemben.
6.ábra: Változatos formájú Donaldson PowerCore™ szűrőbetétek
Picture 6: Donaldson PowerCore™ filters with multifarious shapes
Bild 6: Donaldson PowerCore™ Luftfilterelemente in verschiedenen Ausführungen
II. Az olajszűrésről röviden
A motor működése során számos különböző szennyezőanyag kerül a motorolajba, a szennyezőanyagok a motor üzembiztonságát és az alkatrészek élettartamát csökkentik. A motorolajszűrő feladata a motorolaj tisztán tartása. Csak egy megfelelően előkészített olajfilm képes a száraz-súrlódást megakadályozni. A szűrő az olajat megfelelőképpen tisztán tartja, és gondoskodik arról, hogy egy jó kenőképességekkel bíró olajfilm alakulhasson ki a különböző alkatrészek között. Az olajszűrő szerepe tehát a motorolaj káros frakciójának (abrazív részecskék) kiválasztása, s ezáltal az olaj funkciójának hosszú távon való megőrzése. A motorolajban a szennyező szemcsék mérete nem lehet nagyobb 5 μm -nél. A durva olajszűrők szűrési küszöbe 25-120 μm, a finom olajszűrőké 5 μm alatti.
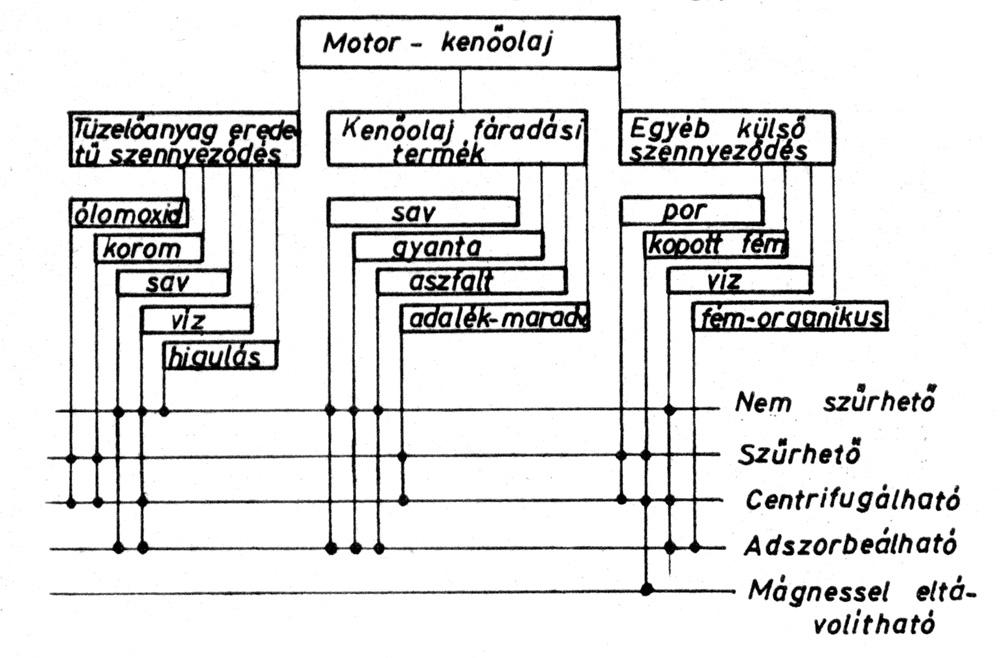
A motorolajban található szennyezőanyagok
7.ábra: A motorolajban található szennyezőanyagok
Picture 7: Impurities in motoroil
Bild 7: Schmutzpartikeln im Motoröl
Minden motorolajszűrő rendelkezik egy ún. bypass, másnéven megkerülőszeleppel. Ez a szelep automatikusan nyílik a szűrő eltömődésekor (duguláskor), amikor is a szükséges olajmennyiség már nem képes a szűrőn keresztül hatolni. A szelep kinyitása után szűretlen olaj áramlik a motorba, ezért nagyon fontos, hogy a szűrő megfelelő szennyeződésfelvevő-képességgel rendelkezzen, s a megkerülőszelep két olajcsere közt lehetőleg ne nyisson ki. A kenési helyekre csak a káros frakciótól mentes olaj kerülhet!
A szűrők fent említett tulajdonsága különbözteti meg a jó szűrőt a gyenge minőségű szűrőtől. Egy elegendő szűrőfelülettel, ezáltal nagy szennyeződésfelvevő-képességgel rendelkező szűrő megkerülőszelepe két olajcsere közt nem nyit ki, legyen szó fémházas szűrőről (csavarpatron) vagy szűrőbetétről.
A motorolajszűrők alapvető fajtái kialakítás szerint: fémházas csavarpatronok, szűrőbetétek. Az olajszűrők a szűrés módja szerint is csoportosíthatók: fémbetétes, papírbetétes, aktív, mágneses, centrifugális, stb. olajszűrők.
Függetlenül attól, hogy fémházas csavarpatronról (spin-on szűrőről) vagy szűrőbetétről van szó, a velük szemben támasztott minőségi követelmények ugyanazok:magas leválasztási fok, hosszú élettartam, egyszerű karbantartás.
Bizonyos alkalmazási területen a motorgyártók mellékáramkörű szűrőt használnak a motorolaj különösen finom szűrésére. Mint a szűrő neve is jelzi, ezek a szűrők mellékáramkörben kerülnek beépítésre, s a szivattyú által szállított olaj kis részét szűrik igen hatékonyan. A mellékáramkörű szűrők nem rendelkeznek megkerülő szeleppel, miután a főszűrőn keresztül az olaj áramlása szűrten vagy szűretlenül, de állandóan biztosított. A mellékáramkörű szűrők képesek a motorolaj élettartamát meghosszabbítani, amelynek elsősorban a magas abrazív tartalmú (2 mikron alatti részecskenagy-sággal telített) környezetben dolgozó motoroknál van igen nagy jelentősége.
III. A modern vasúti dízelmotorok üzemanyagszűrői
Bár a dízelmotorok robusztus és erős gépként élnek az emberek tudatában, üzemanyagadagoló-rendszerük érzékenységét mégsem szabad lebecsülni. A tartós és problémamentes üzemeltetésükhöz elengedhetetlen a gázolaj tisztasága. Az üzemanyagszűrésnek biztosítania kell azt, hogy az üzemanyagellátó-rendszeren keresztül ne kerülhessenek be olyan szennyezőanyag-részecskék a motorba, amelyek a befecskendező rendszer elemein, illesztési hézagaiban kopást, sérülést okozhatnak vagy a porlasztófuratok dugulását okozhatják veszélyeztetve ezáltal a dízelmotor üzembiztonságát
A dízelüzemanyag tisztasága főleg a legújabb generációjú motorok nagynyomású adagolóinál rendkívül fontos. Ez elsősorban abból adódik, hogy a befecskendezési nyomás egyre magasabb lesz. A legújabb adagoló rendszerek (mint pl. a common-rail) már 2000 bar nyomáson dolgoznak, és ez az érték valószínűleg a jövőben tovább emelkedik. Ezek a befecskendező rendszerek a szűréstechniká-val szemben is magas követelményeket támasztanak.
A szennyezőanyag-részecskék kiszűrése önmagában azonban nem jelenti a tökéletes megoldást. A nem kötött víz kiválasztása legalább olyan fontos, miután a vízcseppek az érzékeny porlasztócsúcsok-ban mérhetetlen károkat okozhatnak. A dízelüzemanyag szabvány szerint történő előállításakor 100 kg (= kb. 109 l) 21 gramm vizet és 2,5 gramm szennyeződést tartalmazhat. Ehhez a tartalomhoz jön még a képződött kondenzvíz mennyisége.
A dízelmotorokon alkalmazott üzemanyagszűrők feladatuk szerint lehetnek előszűrők, durvaszűrők, finomszűrők és végszűrők.
Az üzemanyagszűrők alapvető fajtái kialakítás szerint lehetnek fémházas csavarpatronok, szűrőbetétek. Függetlenül attól, hogy fémházas csavarpatronról (spin-on szűrőről) vagy szűrőbetétről van szó, a velük szemben támasztott minőségi követelmények ugyanazok: magas leválasztási fok, hosszú élettartam, egyszerű karbantartás.
A gázolaj szűrése alapvetően két módon történhet: a nyomóágban (az üzemanyag-tápszivattyú után) főszűrőkkel, a szívóágban (az üzemanyag-tápszivattyú előtt) előszűrőkkel.
A gázolajszűrők alapvetően hasonló felépítésűek, mint az olajszűrők, két dologban mégis eltérnek azoktól. Egyrészt az üzemanyagszűrők alapvetően finomabb szűrőanyaggal készülnek, mint az olajszűrők, másrészt az üzemanyagszűrőkbe nem építenek megkerülő-szelepet. A szűrendő részecskék mérete a fejlődés előre haladtával egyre csökken, ma már nem ritkák az olyan motorok, ahol a fő gázolajszűrő 2-5 μm-es nagyságrendig szűr.
Mivel az élettartam – mint említettük – igen fontos szempont, és mert a standard gázolaj minősége a szilárd szennyeződések és a nem kötött víz miatt nem mindig megfelelő, napjainkban szinte minden esetben gázolaj-előszűrőket alkalmaznak. Ezek feladata a fő szűrőbetét tehermentesítése és az üzemanyag lehetőség szerinti teljes víztelenítése. A gázolaj előszűrő készülékek nagy biztonságot jelentenek az üzemanyagellátó rendszer számára, és jelentősen hozzájárul az üzemeltetési költségek csökkentéséhez és a környezet védelméhez.
Az előszűrők működési elve gyártótól függetlenül meglehetősen hasonló, mégis talán a leghatéko-nyabb készülék a több gyártónál (pl. MTU, MAN) elterjedt Separ 2000 berendezés. A SEPAR 2000 egy mechanikus vízleválasztással és szűrőbetéttel kialakított gázolajszűrő-készülék. A H és HZ jellel ellátott típusok elektromos fűtéssel készülnek. A fűtés teljesen automatikusan működik.
A működési elve egyszerű, mégis nagyon hatékony. A leválasztási- és tisztítási folyamat egy olyan szabadalmaztatott rendszer szerint zajlik, amely az összes típusnál azonos. A SEPAR 2000 az üzemanyagrendszer szívóágába, a tartály és a tápszivattyú közé kerül beépítésre. Az üzemanyag a két bemeneti nyílás egyikén át kerül a készülékbe, a nem használt bemenet zárva marad. Első lépésben a bemeneti nyílás felől áramló üzemanyag a belső terelőszárnyakon keresztül intenzív forgó mozgásba kezd. A keletkező centrifugális erő hatására a vízcseppek és a nehezebb szennyezőanyag-részecskék az ülepítőpohár aljára kerülnek és ott összegyűlnek. A külső terelőszárnyakon a kis vízcseppek és a finom szilárd részecskék gyűlnek össze. Ezek az összegyűlt kis részecskék először egymáshoz tapadnak, majd lesüllyednek a pohár aljára a többi részecskéhez. Az üzemanyag felemelkedik a szűrőbetéthez, ahol a megnövekedett keresztmetszet hatására a gázolaj megnyugszik, és így a legkisebb cseppek és részecskék is kiválasztódnak. Ez a négy lépcső a víz és a szennyezőa-nyagok nagy részének leválasztását és a pohár aljában történő összegyűjtését eredményezi. Így a szűrőbetét élettartama jelentősen megnő. Az üzemanyag átáramlik a cserélhető szűrőbetéten. Az egyedi szűrőanyag a még meglévő szabad víz és szennyezőanyagok teljes kiválasztását teszi lehetővé. A szűrőbetét különböző finomságú változatokban létezik (10 vagy 30 μm). A megtisztított üzemanyag két lehetséges úton távozhat a tápszivattyú irányába. A nem használatos nyílás zárva marad.
8.ábra: Vasúti alkalmazásokra szánt duplex kialakítású SEPAR 2000 és a berendezés működési elve
Picture 8: Operational method of SEPAR 2000 and the duplex version for rail engines
Bild 8: Funktionsschema der für Eisenbahnanwendungen entwickelter Separ-2000 Duplex-Anlage
A SEPAR 2000 előnyei: hosszú élettartamú, magas hatékonyságú szűrőbetét, kompakt forma, egyszerű szerelhetőség, nagy fűtési teljesítmény automatikus szabályozással, az indítási problémák megakadályozása nagy hidegben, az üzemanyagban lévő víz hatékony leválasztása (a TÜV vizsgálata szerint víz nem mutatható ki a készülék után), a SEPAR 2000 védi az adagolót és a motort, a SEPAR 2000 karbantartási igénye minimális. Separ 2000 használatával a hideg időben jelentkező gázolaj-problémák elfelejthetők!
IV. Hidraulika, hidrosztatika és kenőolaj szűrés a gyakorlatban
A hidraulika kifejezést a görög „hydro” = víz és „aulos”= cső szavakból eredeztetik. Ma mindazon műszaki tudást kell hidraulika alatt értenünk, amelyek különféle erőknek és mozgásoknak folyadék segítségével történő átvitelével és irányításával függenek össze. A leggyakrabban alkalmazott hidraulikus technika az olajhidraulika (ásványolaj, szintetikus olaj, növényolaj vagy emulzió segítségével). A hidraulika azon az elven alapul, hogy a folyadékok nem összenyomhatók, s így az erőátvitel aránylag kis veszteségekkel (pl. súrlódás) valósul meg. Az utóbbi két évtizedben a hidraulika fejlődése rendkívül dinamikus volt. A gépek mozgása egyre gyorsabb, az átvitt erő egyre nagyobb lett. Ezenkívül a mozgások is mind bonyolultabbá, összetettebbé váltak. A mai hidraulikában nem ritka a különböző mozdulatok és teljesítmények egyidejű végrehajtása.
A mai járművek hidraulikus kormányművel, a munkagépek, mozdonyok hidrosztatikus hajtással készülnek. A hidraulika életünk részévé vált. A hidraulika ilyen dinamikus fejlődéséhez természetesen szükség volt egyre pontosabb vezérlőegységekre is, mint például szervo- és proporcionális szelepekre. Ezeknek a precíz vezérlőegységeknek, valamint az egzakt módon működő szivattyúknak, dugattyúknak és hidromotoroknak viszont nagyon tiszta energiaátviteli közegre, magyarán folyadékra van szükségük.
A tisztasági osztályok meghatározásának alapja a pontosan meghatározott nagyságú szennyező-anyag-részecskék maximálisan megengedett száma egységnyi folyadékban. A szűrőkkel szemben támasztott egyik legfontosabb követelmény a magas leválasztási fok. Ez gyakorlatilag annyit tesz, hogy a szűrőnek a megadott szűrési finomságnak megfelelő nagyságú ill. annál nagyobb szennyezőa-nyag-részecskéket a lehető legmagasabb százalékos arányban ki kell szűrnie a hidraulikus folyadék-ból. A leválasztás fokának meghatározásához alkották meg a szakemberek a b-érték fogalmát. Ez az érték százalékban juttatja kifejezésre egy adott nagyságú ill. annál nagyobb részecskék leválasztásá-nak fokát a szűrőben. A b-érték a szűrő előtt és a szűrő után egy pontosan meghatározott időpontban és differenciál-nyomásnál összeszámolt részecskék számából adódik.
Egy példa: 100 ml folyadékban a szűrő előtt 100.000 db 10 mikron vagy annál nagyobb szennyeződés található, a szűrő után viszont csak 1000 db. b = 10 m = 100 x (100.000/1000)
Ez a b-érték azt jelzi, hogy az összes 10 mikron ill. annál nagyobb szennyezőanyag-részecske 99 %-át ez a szűrő leválasztja (kiszűri).
Az egyre pontosabban dolgozó szelepek, az egyre magasabb nyomásértékek mind-mind finomabb és pontosabb szűrőanyagokat követelnek meg. Ezeknek a szűrőknek működésük teljes ideje alatt garantálniuk kell az előírt tisztaságot.
A szűrőanyagok kiválasztásában elsősorban az alkalmazott hidraulikus folyadéknak van szerepe. Az ásványolaj szűréséhez más szűrőanyagra van szükség, mint például a poliglikol-oldatéhoz. Megkülönböztetünk tehát külső és belső szennyezőanyag-forrásokat. Ezekhez társulnak még az oxidációs folyamatokon keresztül megvalósuló vegyi elváltozások. Képződhet kondenzvíz a rendszerben, amely a hidraulikus folyadék élettartamára van negatív hatással. A fémes szennyező-dések nem csupán mechanikus úton fejtik ki hatásukat, hanem katalitikus úton a folyadékok idő előtt elöregedését segítik elő..
A kenőolaj jelentősége és működése
A kenőolaj feladata a súrlódás megakadályozása és a különböző alkotórészek egymáson siklásának lehetővé tétele, illetve biztosítani kell az egymáson sikló alkotórészek hűtését.
A kenőolajjal szemben támasztott tisztasági követelmények – hasonlóan a hidraulikaolajéval- gyorsan nőttek. A golyóscsapágyak illesztései az egyre nagyobb igények kielégítése végett egyre pontosabbak lettek; a meghajtások fogaskerekei is egyre precízebben kapcsolódnak egymásba az egyre emelkedő fordulatszámok biztosítása céljából. Ma már a konstruktőrök – a hidraulikához hasonlóan – pontosan előírják a kenőolaj tisztaságát. A hidraulikával ellentétben a kenéstechnikában magas vagy nagyon magas viszkozitású olajakat alkalmaznak. A szűréstechnikában ez a magas viszkozitás különösen nagy figyelmet igényel a megfelelő szűrő kiválasztásakor. Biztosítani kell, hogy a kenőolajat akkor is kis differenciálnyomással lehessen szűrni, ha az még üzemi hőmérsékletét nem érte el. Felépítésüket tekintve a hidraulikában alkalmazott szűrőkkel egyeznek meg a kenőolaj szűrők.
Modern kompresszortechnika napjaink korszerű vasúti járműveiben
Biztonsági, hatékonysági és gazdaságossági szempontok alapján bizton állíthatjuk, hogy a sűrített levegővel működő fékrendszerek jelenleg az egyetlen ésszerű megoldást kínálják a vasút számára. Megszámlálhatatlan előnye mellett a néhány hiányosságának kiküszöbölésére irányulnak a fejlesz-tések, mindezeket úgy alkalmazva, hogy sem az üzembiztonság (ezáltal a közlekedésbiztonság) ne sérüljön, sem pedig a költségek (karbantartás, üzemeltetés) ne rugaszkodjanak el a valóságtól.Napjainkban egyre erősödő világszintű tendencia, hogy mind az új beépítéseknél, mind pedig az átépítéseknél (cseréknél) a korábbi csavarlégsűrítők, majd olajos vagy olajmentes dugattyús légsűrítők helyett ún. rotációs légsűrítők kerülnek beépítésre. A váltás oka, hogy a korábban alkalmazott berendezésekre jellemző az üzemidőhöz mérten nagy karbantartási igény, gyakori (nagy számú) meghibásodás, a szakaszos üzem, a viszonylag magas zajkibocsátás és vibráció. A Hydrovane Transit rotációs légsűrítők a legmodernebb technológiával fejlesztett berendezések, melyeket speciálisan a vasúti és közúti járművek igényei szerint hoztak létre. Felépítéséből adódó előnyeit az alábbiakban tekintjük át:
Működési elve miatt képes a folyamatos üzemre, ami fokozott biztonságot jelent a fékrendszereknél, hiszen folyamatos, stabil nyomást biztosít a rendszerben. Csak egy forgó alkatrésze van, nincsenek ékszíjak, egyéb kopó/forgó alkatrészek, azaz minimális a karbantartási költsége és igénye. Ugyanezen okból meglepően csendes ( ≤74 dBA, 1 méter távolságban) és vibráció mentes. Alacsony tömegű és kis helyigényű. Gyakorlatilag egy keretre szerelve bárhol, bármilyen pozícióban beszerelhető a szűk mozdonybelsőben. A kilépő levegő hőmérséklete utóhűtő nélkül is 20 °C alatt marad.
A kialakításkor elsődleges igényként merült fel – a hatékonyság mellett – a jó elhelyezhetőség, emiatt az amúgy is kicsi berendezésbe minden szükséges kiegészítő egységet integráltak. A sűrített levegő előkészítésnek nagy jelentősége van az ezzel működő berendezések élettartamára és üzembiztonsá-gára. A legnagyobb problémát a levegőben jelen lévő víz okozza. Kulcskérdés a vonatok üzembiztos működése érdekében a sűrített levegő víztartalmát a lehető legalacsonyabbra csökkenteni. A levegő előkészítés kiválasztásakor a kompresszor méretezésénél már tapasztalt korlátba ütközünk: a mozdony zsúfoltságába. Ezt figyelembe véve a lehető leghelytakarékosabb megoldást kell választanunk. Ideális megoldás a membránszárító. A membránszárítót kis kompakt egységként telepíthetjük a kompresszor alapkeretére (lásd. a képen), elektromos bekötést nem igényelnek. Hasonlóan kis helyigénnyel rendelkezik a sűrített levegő olaj, és egyéb szennyeződés tartalmát csökkentő szűrő kombináció is, amely védi a teljes levegőrendszert, és a membránszárítót is. Az olaj és szemcseleválasztás két lépcsőben (0,1 ill. 0,01 μm) történik. A membrán szárító a sűrített levegő harmatpontját 20 – 50 °C-kal képes csökkenteni. (pl. 35 °C –os 6 bar-os levegő víztartalma 6 g/m3. Ezt a mennyiséget membránszárítóval akár 0,18 g/m3 – re tudjuk redukálni.) Ezáltal csökkenteni tudjuk a mozdony, és a teljes szerelvény korróziós terhelését, azaz nagyobb üzembiztonsággal, és kisebb javítási költségekkel tudunk kalkulálni, illetve teljesen megszűnnek a jelenleg előforduló téli szétfagyásos problémák.
A Hydrovane kompakt kialakítású egységeit jelenleg a világ minden táján alkalmazzák, mind vasúti, mind földalatti környezetben.
Felhasznált Irodalom:
Othmar Schneider: Szűréstechnikai alapismeretek (kézirat)
Dr Nagy László – Vasúti járművek, diesel-motorok
Dr Dezsényi György, Dr Emőd István, Dr Finichiu Liviu – Belsőégésű motorok tervezése és vizsgálata
www.donaldson.com
www.fundinguniverse.com
www.afssociety.org
www.highbeam.com